ピッキングを効率化させるために始めたいこと
公開日:2018年03月29日
更新日:2018年03月29日
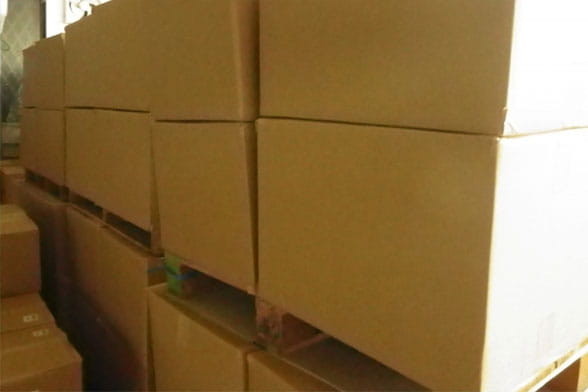
注文を受けた商品を発送するにあたり、出荷指示書を元に棚などから商品を取り出す作業をピッキングといいます。
今回は、ピッキングの効率化についてご紹介します。
ロケーション管理にはどのような種類があるのか、また、ロケーション管理はネットショップにどのような効果をもたらすのか、その重要な役割についてご紹介します。
ピッキング作業の基本
ピッキング方式には大きく分けて摘み取り方式と種まき方式の2種類があります。それぞれの特徴を見てみましょう。
摘み取り方式
出荷先やオーダーごとに棚から商品を集めて梱包して出荷する方式です。木から実を摘み取るような作業スタイルなので摘み取り方式と呼ばれます。
メリットは、商品をピッキングしたら梱包・出荷までを素早く行えることです。
デメリットは、商品数にあわせた棚の設置を行うため、広いピッキングスペースが必要となり、作業者の移動距離が長く時間がかかることです。出荷先は多いものの出荷数が少なく、扱う商品の種類が多い場合にマッチします。
種まき方式
商品を一旦、必要な数だけピッキングして荷捌き場に集め、その後、出荷先別に分ける方式です。さまざまな種を畑に植えていくように仕分けるので種まき方式と呼ばれます。
メリットは、複数の出荷先やオーダー分の商品をまとめて集めるため、作業者の移動距離が短く、効率的に作業ができることです。
デメリットは、管理者以外に作業の全体像が把握しづらいこと、追加注文が発生したときなどに対応が大変になること、荷捌きをするスペースが必要なことです。出荷先の数が多くなく、少ない種類の商品を一度に大量出荷する場合にマッチします。
ピッキングで発生しやすい無駄って?
ピッキングには、待つ、考える、移動する、探す、取るという5つの無駄が発生すると言われます。
いつでもピッキングができる状態なのにピッキングリストが発行されずに待つ、該当商品がどの棚にあるか考える、出荷頻度が高い商品なのに遠い場所にあるためにそのたびに長い距離を移動する、どこに商品があるかわからず探す、高い場所に置いてあって商品を手に取るのに台を使わなければならない……など、これらはすべて種類の異なる無駄です。
ピッキングを効率化するには、この5種類の無駄ができるだけ発生しないよう工夫します。
ピッキング効率化のための心得
無駄をなくすには倉庫内の棚や検品台、梱包台などのレイアウトを見直し、作業導線を最適化しましょう。またスタッフの役割分担や配置を含めて、作業フローがスムーズに進むような改善も行います。在庫管理システムを導入することも、正確さや業務スピードが高まることを含めて、非常に効果があります。
しかし、その前に行いたいのは、自社商材の特徴・特性を分析し、どのような考え方に基いてピッキングの効率化を実現するのか、青写真を描いておくことです。上述のピッキング方式は販売方法、出荷数、出荷先の数、商品の種類の多さ、回転率、受注ロットなどによって適した方式を選択し、その他の自社の事情に合わせてアレンジを加えていくことになります。以降も定期的な見直しも必要となっていきますが、繁忙期があればその間にどのように体制を強化するか、将来、売上規模が拡大したときにはどのようにスペースを確保するかも考えておきましょう。
ピッキングの効率化は商材特性や販売方法と連動させて考えるのが基本です。仕入れ、在庫管理、販売という一連の流れを考えながら、ミスの発生が無く、その全てがスムーズに流れていくような効率化を目指した仕組みを作り上げていきましょう。
まとめ
ロケーション管理は単に倉庫内のピッキング作業を楽にするためだけのものではありません。ロケーション管理によって在庫管理を効率化させることによって、更なる売上拡大や顧客満足度向上を目指すことができるネットショップを作り上げていきましょう。